Как производят ламинированную фанеру
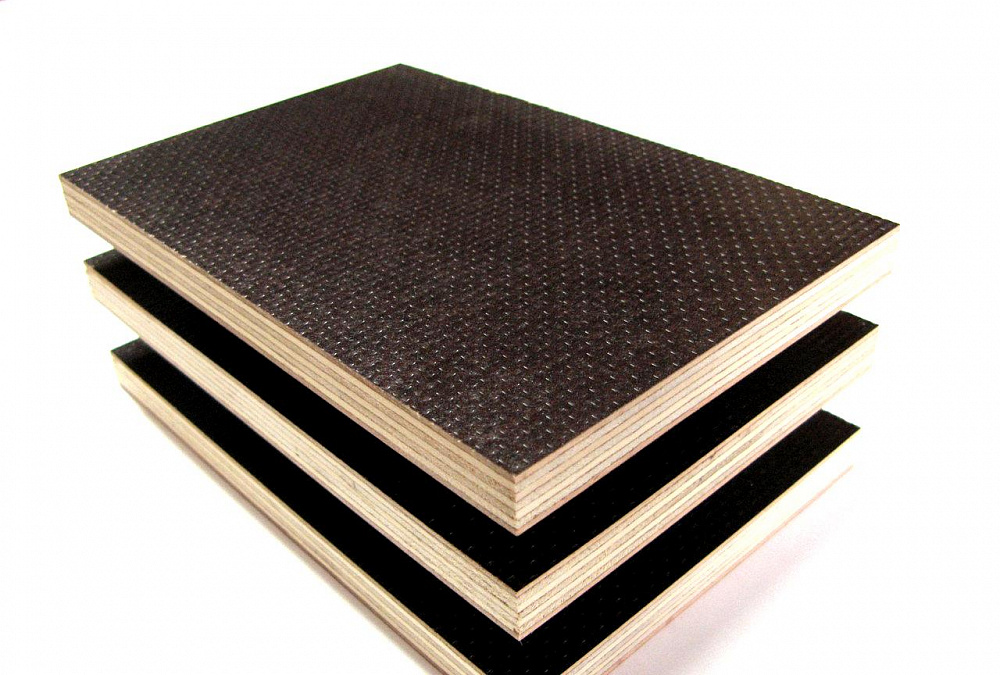
Поэтапное производство ламинирующей фанеры
В связи с тем, что приобрело популярность монолитное строительство – возведение дома из арматуры и бетона – стали распространяться опалубочные системы. Они представляют из себя конструкции, поддерживающие с помощью щитов правильную форму бетонному объекту.
Опалубка состоит из металлического каркаса и ламинированной фанеры, которая за счет своей гладкой, ровной поверхности, с хорошо прокрашенными торцами, допустима к многократному использованию.
При производстве ламинированной фанеры важно с точностью придерживаться рецептуры, поэтому этот процесс считается сложным и многоступенчатым.
Группа “Свеза” является мировым лидером по изготовлению березовой фанеры, на ее примере изучим процесс производства продукта, стойкого к воде и механическим повреждениям.
Немного из истории:
Изобретатели первых станков по изготовлению фанеры связаны с Россией. Эта конструкция была запатентована в XVIII веке и заключалась в переработке натуральной древесины в тонкие листы, а потом превращении их в фанеру.
За 300 лет технология переработки не была изменена, но произошла модернизация станков, в результате чего доля ручного труда сократилась и уступила автоматизации. Такой шаг упростил процесс изготовления материала и повысил его качество.
Материалы, используемые при ламинировании фанеры
- Меламин – основание, содержащие меламиноформальдегидные смолы, которые создают прочное водонепроницаемое покрытие.
- Фенол – это простейшее соединение из класса фенолов, являющееся частью органических смол, применяемых в изготовлении деревянной фанеры.
- ПВХ – самый популярный материал для ламинирования, обладающий хорошими технологическими характеристиками и низкой химической активностью.
Начальный этап. Заготовка сырья
- Для начала тщательно подбирается необходимое сырье (деревья с подходящим диаметром стволов и высотой). Например, привычный размер для фанеры, производимой в России – 1,22x2,44м. Для такого формата используют деревья с диаметром 0,2-0,4 м и 5,2 м в длину. В процессе изготовления их пилят на чурки по 1,3 м или 2,6 м в зависимости от желаемого конечного размера.
- Далее идет обработка сырья горячей водой, проходящая в открытом или закрытом бассейне в течении суток. Летом проварка идет при температуре 45-40 °C, а зимой при 40-45 °C. Чтобы шпон не утратил качество, важно соблюдать рекомендуемые температуру и время обработки.
Обработанный высокими температурами фанерный кряж – отрезок нижней части ствола – поступает в отделение по окорке (удалении коры и луба с поверхности кряжа) и распилу.
- При окорке специальные ножи, встроенные в станок надрезают и сдирают слой коры. Когда кряж освобожден от луба и коры, он поступает на металлодетектор, который проверяет на наличие в древесине металлических остатков (гвоздей, проволоки, скоб и т.д.). Это делают для того, чтобы оборудование не вышло из строя при контакте с инородными телами. Если обнаружен металл, прибор дает сигнал, процесс приостанавливается и металлические включения удаляются.
Интересный факт! Снятая при окорке кора используется в качестве топлива для комбината и окружающих его зданий, иногда поселка. Например, Пермский фанерный комбинат обеспечивает свою котельную, а также Уральский поселок, где он находится.
- Следующим шагом выполняется распил – членение обработанного сырья на куски для изготовления шпона с поперечным и продольным сечением.
Второй этап: производство и обработка шпона
- Происходит лущение шпона – нарезание поперек древесины заданной толщины. Чем тоньше будут эти пласты, тем большее их количество понадобиться для изготовления фанеры. Прочность и толщина конечного материала зависит от количества слоев. Если сравнивать березовый шпон с другими породами деревьев, то он самый тонкий, 0,012-0,015 м, в то время, как из хвойных деревьев – от 0,02 до 0,04 м, а из тополя – 0,016-0,026 м.
- Лущильный станки настраиваются исходя из ряда параметров шпона: толщины, плотности. На контроле качества выбирают образцы, изучают их и полученные показатели сравнивают с установленными нормами.
- После разрезания древесины полученные ленты идут на прибор, где их рубят по размеру 1,3x2,6 м, чтобы изготовить фанеру 1,22x2,44 м. Продольный и поперечный шпон производят отдельно, а впоследствии склеивают для получения одного фанерного листа.
- Шпон, разрезанный на листы определенного размера, поступает в сушилку, где обдувается потоком горячего воздуха. Таким образом, находясь там в среднем 10 минут теряет более половины лишней воды.
При выходе из сушилки шпоночные листы укладывают на погрузочную плиту или транспортное средство для крупногабаритных грузов (транспортер). - Следующим шагом происходит отсортировка шпона по показателям: количество трещин, расколов, сучков, заноз и других неровностей, а также определяется степень влажности. Для этого поверхность сканируется и прибором выдается оценка, исходя из которой он сортирует шпоны по стопам. С целью упрощения процесса используют автоматические станки с заложенными через компьютерную программу параметрами, а оператор только следит за работой машины.
- Если на сортировке шпон оказался с повышенной влажностью, то его сортируют отдельно и позже проводят повторную сушку.
Если выявлены дефекты, то листы отправляют на починку, которая может проходить как вручную, так и на автоматизированных станках. Автоматизация помогает в разы улучшить качество, сократить затраченное время и силы. Существует оборудование как для большого формата шпона – 1500x3000 мм, 1525x3050 мм, так и для базового 1525x1525 мм.
После устранения дефектов листы древесины снова проходят сортировку.
Этап формирования фанеры
- На этом этапе шпоночные листы склеиваются, образуя фанеру. Прочность и стойкость к механическим воздействиям готовому продукту придает перпендикулярное расположение волокон в соседних слоях. Это свойство делает возможным применение фанеры в конструкциях для поддержания бетонированных объектов в монолитном строительстве.
- Березовую фанеру производят путем склеивания нечетного количества шпоночных листов 3-40 мм в толщину. Скрепляются они при помощи специального клея, приготовленного в производственных условиях с использованием смесителя. В его состав входит мел, вода, смола, ржаная или древесная мука. Главное в наведении клеящего состава – соблюдать пропорции, чтобы готовый продукт не дал трещин и расслоения. Для этого созданы специальные машины, которые контролируют количество ингредиентов, поступающих в смесь.
- Следующий шаг – вальцовка – прохождение листа шпона между валиками, намазанными клеем. С помощью такой установки каждый лист равномерно покрывается клеящим составом, а затем отправляется в стопу наборного пакета. Там клеевые листы поочередно кладутся на сухие, пока фанера не станет нужной толщины.
Чтобы две соседние фанеры не склеились между собой, автомат выдает подряд два сухих листа, а далее по аналогии. Полученную стопу отправляют на подпрессовку.
- Сначала фанера подвергается холодному прессованию для получения цельных пакетов, которые удобно будет транспортировать и подвергать горячей прессовки. На этом этапе прессовка происходит под давлением 1-1,5 МПа не более десяти минут. На горячую прессовку листы собирают в этажерку для финального скрепления под давлением 1,2-1,8 МПа и температуре 120-130 °C.
- Подверженные прессовке листы обрезают под нужный заказчику формат (1,25x2,5м, 1,22x2,44м) с отступлением от него не более, чем на 3 мм. При изготовлении ламинированной фанеры станком обрезают на 40 мм меньше, чтобы после нанесения пленки была возможность срезать лишнее.
- Чтобы поверхность фанеры не имела сучков и шероховатостей, была ровной, ее подвергают шлифованию на лентах разной зернистости. Далее фанера снова проходит классификацию по внешнему виду, который оценивается оператором.
Завершающий этап: покрытие ламинирующей пленкой
На каждый фанерный лист наносится пленка с обеих сторон, а потом практически готовый продукт отправляется в многопролетный пресс, куда помещается до 18 листов одновременно. В результате прессования, которое происходит при температуре 130-160 °C пять-десять минут (в зависимости от структуры пленки и покрытия) пленка плотно обволакивает поверхность. Фанера за счет этого становится стойкой к механическому воздействию, агрессивной окружающей среде и повышенной влажности. Таким образом, обычная белая необработанная фанера превращается в ламинированную.
Вместо глянцевой пленки часто используют покрытие в виде сетки, обладающее противоскользящим эффектом. Области применения такой фанеры:
- в строительстве транспорта, например, для укладки пола в трейлерах и легковых автомобилях;
- в работе на стройплощадках в роли настилов;
- в складах;
- в качестве стройматериала погрузочных участков;
- при обустройстве детских игровых площадок;
- создание нескользящего пола;
- в ремонтных работах для крупного оборудования;
- из б/у фанеры делают заборы и другие хозяйственные сооружения.
- Следующим этапом происходит обрезка ламинированной фанеры по формату.
- Сортировка по внешним показателям и размерам с последующей укладкой в пачки.
- Фанера попадает в камеру, где происходит ее покраска. Чтобы она не намокла и не разбухла, на ее торцы наносят водоэмульсионную краску с акриловой основой, способной защитить от лишней влаги.
Соответственно, чем лучше прокрасили торцы, тем устойчивее продукт к влаге, что определяет количество циклов заливки бетона, которое фанера выдержит. Этот показатель играет большую роль в опалубке потолка, так как перекрытия подвергаются мощному механическому давлению и нагрузки от бетонной смеси.
Так, количество применений фанеры зависит от качества внутренней склейки, гладкости и износостойкости поверхности, влагоустойчивости, потому что эти показатели влияют на сохранность первоначальной формы продукта. Если качество на высоком уровне, то лист может выдержать 20 циклов, не утратив свойств.
Итог
Ламинированная березовая фанера распространена в монолитном строительстве из-за того, что обладает высокой прочностью, упругостью, стойкостью к большим нагрузкам, прилагаемым к ней при опалубке дома.
Процесс ламинирования непростой, потому что требует соблюдения четких правил. Если их нарушить, то конечный продукт не будет пригоден для строительства, а процесс отделки станет более трудоемким.
От качества фанеры зависит:
- надежность постройки;
- красивый внешний вид;
- рациональное строительство.
Плюсы и минусы ламинированной фанеры
Сравнивая преимущества и недостатки ламинированной фанеры, выигрывают первые и к таковым относится:
- Водостойкость, так как благодаря глянцевой пленке на поверхности и эмульсии на торцах, фанера не деформируется при контакте с водой.
- Покрытие ФСФ препятствует появлению грибка, плесени.
- Стойкость к химическим веществам избавляет строителей от дополнительной обработки продукта перед использованием.
- Ламинированная фанера, в отличии от обычной, стойкая к прямым солнечным лучам и не выгорает.
- Устойчива к поперечным и продольным нагрузкам, ударам, потому что слои укладываются перпендикулярно.
- Применима не только в монолитном строительстве, но и других областях: изготовлении мебели, складского оборудования, машиностроении.
- Хорошая звуко- и теплоизоляция.
- Заниматься монтажом ФСФ можно самостоятельно, потому что этот процесс не сложный.
- Изготавливают разные фанеры разного формата, что делает продукт универсальным.
- Защита от кислоты и щелочи.
Есть и недостатки:
- За счет глянцевой поверхности, к ламинированной фанере сложно что-то приклеить, для этого потребуется чуть больше времени.
- В некоторых случаях плохая проходимость воздуха также является существенным минусом.
- Материал не рекомендуется использовать в помещениях, где находятся дети, потому что в нем содержатся не безвредные фенолы.
- Материалы достаточно дорогие.
Исторические факты
Первая модель станка для получения лущеного шпона была создана Сэмюэлем Бентам в конце 17 века. Ранее он служил Екатерине II, а вернувшись в Англию, запатентовал несколько изобретений. Его лущильному станку производители не придали значения.
По-настоящему эффективный образец современных станков был создан Эммануэлем Нобелем, отцом Альфреда, который создал Нобелевскую премию. В конце 18 века разработан поворотный токарный станок, способный снимать шпон ровным слоем. Эта технология позволила производить фанеру одинаковой толщины и структуры.
В период 1838-56 гг. Нобель жил в России и создавал технику для военной промышленности, к которой с одобрением относился Николай I.
Дитрих Мартин Лютер — русский промышленник, который в 19 веке владел мануфактурой по изготовлению карандашей в Эстонии, изобрел крупногабаритную версию лущильного станка для карандашей. В 1819 году получил патент за него. Первую фанеру, которая прошла этапы обработки на его станке, создал эстонский мебельщик Александр Лютер.
Позже он создал стул, скрепив между собой листы шпона — он получился нетяжелым, прочным и недорогим, что вызвало интерес у людей.
Огнеслав Степанович Костович занимался созданием летательных аппаратов и нуждался в материале для их постройки. В 1881 году он придумал и изобрел фанеру-арборит, которая состояла из перпендикулярно склеенных между собой листов шпона. Клей и станок для обработки также были изобретены Огнеславом. Получившийся продукт обладал влагоустойчивостью, стойкостью к гниению, прочностью.